Background of Indian Textile Industry
One of India’s oldest Industry and the largest employer only next to Agriculture, the Textile Industry was once a Crown Jewel of the Indian Manufacturing Landscape. Textile was India’s first modern industry and an accelerator of growth in the country. However, the Industry has gone through a roller coaster ride over the last few decades starting 1980s, when Mumbai and Ahmedabad were once the hub of the Industry employing a large population of these cities.
Currently the domestic textile and apparel industry contributes 2% to India’s GDP, 7% to industrial output and 13% to Manufacturing Output in value terms. It also contributes 12% to country’s export earnings. India is the largest producer of cotton in the world accounting for about 26% of the world cotton production and the industry continues to be predominantly based on cotton, with about 65% share among the raw materials consumed.
The traditional Indian textile industry is divided into Powerlooms (using machines), Handlooms, Handicrafts and small-scale power-loom units. Powerlooms contributes 60% of total cloth production in the country and more than 60% of fabric meant for export. The readymade garments and home textile sectors are heavily dependent on the Powerloom sector to meet their fabric requirement. The Handloom sector contributes nearly 15% of the cloth production in the country and 95% of the world’s hand-woven fabric comes from India.
Issues with the Indian Textile Industry
Although textile is the one of the oldest industry in India it is not the most advanced, profitable and operationally efficient industry. Several companies have pivoted their businesses from textiles to other industries. Although there were many reasons behind their move, the fact that the Indian textile industry is not as lucrative as it once was, didn’t help. For instance, we all know Phoenix Mills as one of India’s largest mall and real estate developer & operator but it began its journey on the other side of the spectrum, as a manufacturer of Cotton textile goods in 1905, but after 8 long decades the company pivoted its business from that of a mill operator to a real estate operator and developer. Reliance Industries is another behemoth which started out in the textile business but later changed its direction.
There are multiple reasons behind the current state of the Industry but before we move forward and explain the issues at hand, it is important to understand the entire value chain right from raw material sourcing to manufacturing of the final product. Textile products are made from “Fibres” which are derived through the “Ginning” process from Cotton, Silk, Jute, etc. (Natural Fibres) or from Polymers (Man-made Fibres) found in plants, natural gas and the by-products of petroleum. Fibres are then converted into Yarn through a mechanical “Spinning” process. The core of textile manufacturing is the Fabric, which is produced through the “Weaving/Knitting” of the Yarn. The Fabric is further processed based on end use requirements.
Issues
1. Globally non-competitive Value-added products:
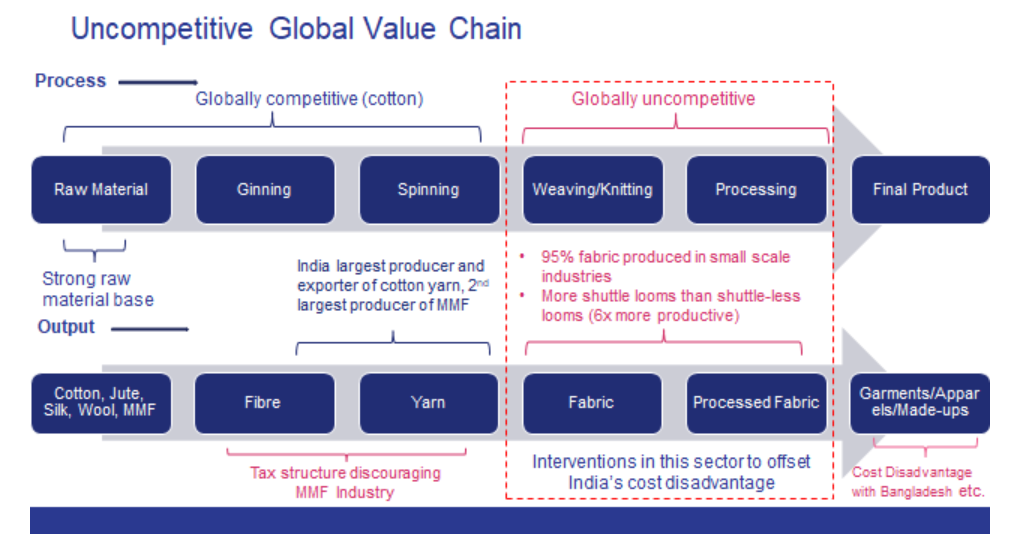
Fortunately for India, when it comes to natural and man-made fibres (MMFs) it has a very strong base. India also has a strong presence in production and global exports of cotton yarn. Because of this richness, India is globally competitive when it comes to production of the raw material and its conversion into yarn.
However, if we go up the value chain, the weakest link of the Indian textile industry is exposed. India contributes marginally when it comes to global export of fabrics with a share of just 5-6%, while China is the leader with a substantial share of 51% in cotton fabrics. The situation is similar in case of MMFs. Even though we’re the largest producer and exporter of cotton yarn we are not globally competitive when it comes to fabrics largely because of the size and structure of our weaving/knitting & fabric producing units along with the outdated technology.
Approximately 95% of the weaving sector in India is unorganized in nature. The processing segment is also dominated by a large number of independent, small-scale units. This section of the value chain face multiple challenges such as inadequate know-how, financial stress, low focus on R&D and innovation, obsolete technology and most of all no economies of scale.
2. Government Policies:
Historically, policies of Indian Government for textile have hardly brought out the best for the industry. In the past, the Government had sought control over the prices, the distribution system of yarn, encouraged proliferation of unorganized sector and the pattern of production in the country. The Raw material sourcing is still covered by the laws of Minimum Support Price which has inadvertently impacted the free market principles.
In 2019, Rebate of State and Central Taxes and Levies (RoSCTL), a new scheme was introduced to make sure the garment exports sector enjoys a continuity in tax benefits under the GST regime. The scheme sought to refund the taxes on inputs paid by the industry but ten months on, however, because of some issues between Ministries of Finance and Textiles, the refunds for the companies were stuck and they had to go through a rough period due to shortage of capital.
Countries like Bangladesh have flourished in last 2 decades and our own export policies were partly responsible. Bangladesh doesn’t have a very strong raw material base like us but our policies for making Indian cotton and yarn cheaper for exports by giving various incentives to exporters helped Bangladesh to produce cheaper Fabrics and in turn made it difficult for our domestic value-adding companies to compete with the neighbour. The entire textiles industry lost money until the export incentives on cotton were removed.
3. Technological Obsolescence
There are approximately 25 lakh Powerlooms in the country and the technology level varies from plain loom to high tech shuttle-less looms (modern looms). It is estimated that more than 75% of the shuttle looms are obsolete and outdated with a vintage of more than 15 years and have virtually no process or quality control devices. However, there has been some upgradation in the technology level of the powerloom sector during the last 8-9 years.
India has one of the largest installed production bases in the world in the weaving sector but it is marred by use of old technology with low quality & productivity and lack of large and modern fabric manufacturers. India has only 2% share in global installed capacity of shuttle-less looms.
4. Financially Sick Units
National Textile Corporation was set up by the Government to take over operations of 124 Sick Mills which were Nationalized. Of the 124 mills, 119 were referred to the Board of Industrial and Financial Reconstruction for financial and operational restructuring. Presently 77 of those mills have been shut down, 2 are not operational, 23 are in operation while other units are being revived under JV route. The government has so far spent more than ₹ 9K Cr on their revival and operations.
Private sector has not done any better, as of Sep 2020, Corporate Insolvency Resolution Process under Insolvency & Bankruptcy Code, 2016 has been initiated against 279 companies in Textile, Apparel & Leather products segment.
Has anything changed?
So now we know the issues within Industry, the question is what has changed over the years that will help it revive? And is it enough to compete with the likes of Bangladesh, Vietnam & China?
Government Initiatives
The focus of the Government in recent time has been on increasing the share of textile manufacturing by building the required modern infrastructure, upgradation of technology, enhancing skills and traditional strengths. Below are some of the schemes launched by the Government –
1. Technology Upgradation: Amended Technology Fund Upgradation Scheme (ATUFS):
With a vision of generating employment and promoting exports through credit linked capital investment subsidies on any Technological Upgradation done in the textile production chain this scheme envisages an outlay of ~₹ 18K Cr to mobilize new investments of about ~₹ 95K Cr and to create new employment for about 35 lakh persons by the 2022. As on January 2020, a total of 9,605 Unique Identification Numbers have been issued under ATUFS with estimated project cost of ~₹ 40K Cr.
2. New Skill development scheme: Scheme for Capacity Building in Textile Sector (SCBTS):
The Textile Ministry has introduced new skill development scheme covering the entire value chain of the textile industry excluding Spinning & Weaving in the organized Sector.
3. Scheme for Integrated Textiles Park (SITP):
SITP has been under implementation to provide the textile industry with world-class infrastructure facilities. The project cost covers common infrastructure and buildings for production/support depending on the needs of the ITP with total financial support of 40% of the project cost subject to a maximum of ₹ 40 Cr. Till now, 56 textile parks which are under various stages of implementation have been sanctioned with ~₹ 1,350 Cr disbursed. Of these 22 parks have been completed.
4. Scheme for Additional Grant for Apparel Manufacturing Units under SITP (SAGAM) and Scheme for Incubation in Apparel Manufacturing (SIAM):
While under SAGAM, the Textile Ministry provides additional grant of ₹ 10 Cr to Integrated Textile Parks under SITP to set up new/additional apparel units in the park, the objective of SIAM is to promote new entrepreneurs in apparel manufacturing by providing them an integrated workspace with complete ecosystem and plug and play facility which will help them in reducing time, cost and efforts involved in setting up a new incubation centre.
5. Scheme for Textile Industry Workers’ Accommodation (STIWA):
The objective of this scheme is to provide safe, adequate and conveniently located accommodation for textile and apparel industry workers in the proximity of areas of high concentration of textile and apparel industries.
Apart from the above mentioned schemes, dozens of other schemes and incentives have been under implementation to support the development of the industry through financial incentives, Export promotion, support for raw material, technological upgradation, infrastructure, R&D, etc.
Government’s “New Textile Policy” has among others envisaged the following for the industry:
- To set up machinery manufacturing hubs via FDI support as we import nearly 75% (₹ 13K Cr) of machinery for the sector
- Textile research institute to be set up in Coimbatore
- Structural shift to make India a man-made fibre (MMF) rather than a cotton-driven industry
- Ministry has identified 50 key sectors such as sanitary napkins and winterwear for the production linkd incentive scheme with a five-year gestation period
- Removal of Anti-dumping duty on PTA (Purified Terephthallic Acid) and acrylic fibre to boost the MMF sector
Announcement in the Union Budget 2021-22:
- Establish 7 Mega Textile park in next three years
- ₹ 10K Cr production linked incentive scheme for man-made fibres and technical textile
- ₹ 3,615 Cr yearly grant to the textiles and clothing sector for various existing schemes.
- Basic customs duty on caprolactam, nylon chips and nylon fibre and yarn will be uniformly reduced to 5%
It is quite evident now that the government is proactively taking multiple steps and initiatives to steer the textile industry in a direction where it’ll be in a position to compete with its global peers. However, it is important to understand that while giving or withdrawing incentives if they are not appropriately measured against their impact it can have a serious cost on the entire industry. For example, when the incentives given for export of cotton yarn that were benefitting Bangladesh were removed and duties were imposed so as to not let foreign importers benefit, it impacted the exports substantially leading to an endless decline (exports are now down more than 50% since their peak in 2013-14).
More recently, certain changes in the Union Budget like the imposition of 10% Customs Duty on import of Cotton which until now was duty-free didn’t go down well with their other announcements. You see although India is the largest cotton producer there are certain niche varieties which are not grown in India and needs to be imported, this will directly impact manufacturers who use this variety of cotton.
The Way Forward
Development and turnaround of the textile industry is the best poverty alleviation program the government can ask for. With women forming 70-80% of the workforce, it is great for promoting women participation in labour force. Knitting/weaving sector is the key link in the textile industry which needs to be strengthened, it consolidation and development will support the domestic spinning industry and also makes our fabric sector globally more competitive.
China and Bangladesh are the largest importers of cotton yarn from India, who in turn creates value addition to the yarn and then exports the same at a lower cost compared to India. It is pertinent for India to flow up the value chain from being a supplier of cotton yarn to a producer of value-added fabrics and garments by strengthening our knitting/weaving sector.
A concentrated, collaborative and supportive endeavour from the government can go a long way in helping the industry. A leaf from our neighbours’ book with some modifications can do wonders. In 2000, Bangladesh’s apparel exports (at 2.6% of global share) lagged behind India’s (at 3%) but a concerted government effort and its ability to leverage duty-free access to markets such as the European Union (giving it an 11% pricing edge over us), has made it the world’s second largest apparel exporter after China.
Post the onset of the pandemic, a great deal of business is getting out of China, supply chains are being reimagined and countries such as Vietnam and Bangladesh have grabbed these businesses with many Chinese manufacturers building new capacities in Vietnam. Even Africa, with low wages is emerging as new low-cost geography. A prime issue with Indian manufacturers and exporters is their size, they are small and fragmented, a fifth of those in Bangladesh, Vietnam and China. Consolidation of small and medium units is a necessity for building a robust Textile Industry.
Case in Focus: Aarnav Fashions
Aarnav Fashions Limited (AFL) is a well-established, BSE-listed company with a market cap of Rs. 135 crores, in the field of textile fabric-suiting manufacturing. It is a part of one of the leading textile houses in India, based out of Ahmedabad, Gujarat, growing under the able guidance of Shri Champalal Agarwal, an industry veteran with over 4 decades of experience in the textile space. What started as a small family set-up, under the name Omkar Group, has grown significantly over the years. Company operations have evolved with strategic backward and forward integration, along with a dynamic improvement of its infrastructure and machinery. In FY20, AFL generated a revenue of ₹ 35 Cr, and a PAT of ₹ 2.3 Cr.
The company deals in shirting, dressing, ladies, and kids wear and home furnishings and has been successfully exporting its products to Sri Lanka, the Middle East, Europe, East Asia and the USA. It sells its products across the country via agents, brands and its own network.
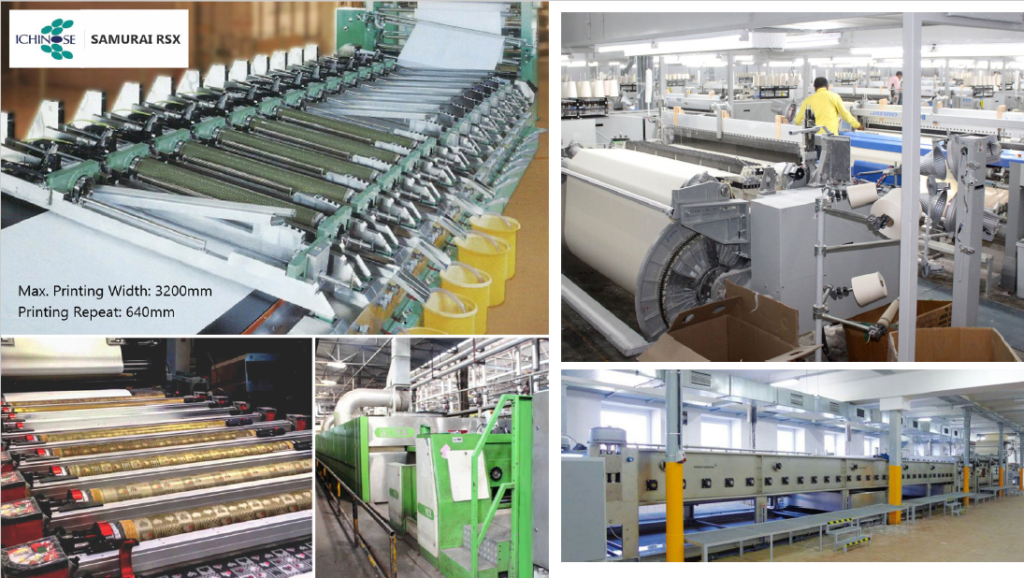
What makes AFL an interesting case in point is the reverse merger/consolidation of 6 group companies, which might be the first move towards the much-needed consolidation in the textile industry.
The Reverse Merger Decoded
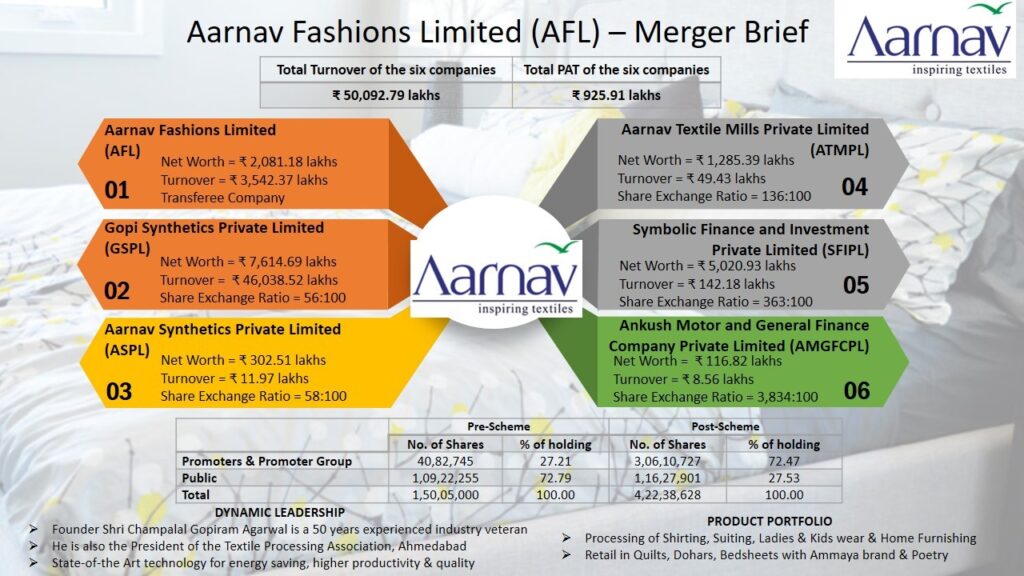
The consolidation entails merger of 6 companies – Aarnav Fashions, Gopi Synthetics, Aarnav Textiles and Aarnav Synthetics all of which are into textile processing and manufacturing. While Symbolic Finance business revolves around textile trading and Ankush Motor and General Finance are the investment holding company for Symbolic Finance.
The factory premises of the consolidated entities is in Narol, Ahmedabad, spread over 15 acres with a built-up area of 1 million sq-ft. It’ll have eight rotary printing and six flatbed printing machines from leading makers such as Osthoff, Toyota, E-Shades, SPG, and Menzel, with a printing capacity of 225000 square meters per day, and a dyeing capacity of 75000 square meters per day and a weaving plant with 112 looms. Apart from key management personnel, the Group employs 1300 workers and 200 team members.
The group now has the capacity to process sizeable orders with high quality outputs and specifications as per the requirements of the clients, at competitive prices and reasonable deadlines. Management guidance has been positive, and the group is targeting a 10-15% increase in revenue Y-o-Y, through capacity expansion and modernisation. Post consolidation, the group will have an estimated revenue of ₹ 500+ Cr, and an estimated PAT of ~₹ 10 Cr.
The consolidation of Aarnav Fashion Ltd although within the same group, throws light on the much-needed consolidation in the textile industry. It can play the role of a torchbearer for the trend of consolidation and help in making the textile India’s crown jewel once again.
For Sources Click Here
Disclaimer:
We, Anosh Mody & Priyank Jain shall take no responsibility for any profit or losses occurring out of investment/trading decisions you make based on the contents of this article.
We are not SEBI registered investment advisors. This article is meant for educational purposes only, please consult your investment advisor before acting upon any information you see here.
Anosh Mody is an MBA student from SBM, NMIMS Mumbai and Priyank Jain is an Investment Analyst at a Distressed PE Fund. However, the views reflected in this article are strictly their own, and in no way reflect upon the B-School and the Fund in any manner.
Follow Us @
Sources
1. Cotton Corporation of India.
2. https://niti.gov.in/weaving-way-indian-textile-industry.
3. Ministry of textiles.
5. Arnav Fashion Investor Presentation
Wow. Seem to be 2 months late, for reading this. Stock has literally taken off a 2x level from Jan’21….hats off guys, for the good work